Using new technology to revitalise old equipment
Keeping costs down by extending the life of old equipment has it’s own challenges
Even when parts are readily available. But for one operator in the midlands, keeping their road/rail stock going was becoming a bigger problem. All the control gear and hydraulics used in the fleet had been made obsolete, pushing a number of older vehicles in the fleet to being beyond reasonable repair. Entire systems would need to be ripped out and replaced.
Rather than seeing the issue as a problem, they embraced the opportunity to learn how the latest developments in control technology and best practice could help them take their products to the next level.
Queue Eaton Hydraulics and their Lean Automation Partner, DAJO Solutions. Together they were able to exceed the customer brief and expectation in a number of areas.
First, by implementing modular systems and controls they massively reduced the amount of physical wiring, as well as the associated commissioning time. Additionally, automated systems enhanced driver safety and that of others in the vicinity of the vehicle. Finally, spare capacity within the system for additional inputs and outputs enabled flexibility and future proofing of the vehicle that had not previously been available. All this was achieved in a fraction of the time, and at a fraction of the cost of replacing the original plant.
Andrew Barlow, DAJO Solutions senior engineer said. “Initially the client was sceptical about moving to a software based solution. But, after seeing the time and cost savings, the support integral to our package, and to be able to give their customers a more complete, comprehensive solution alongside massive savings, they decided the risk was worth it.”
About the Application
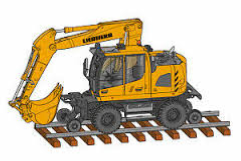