Do you know which quality management system is best for you?
How do you measure quality?
Understanding and quantifying how good you are at a particular aspect of your business is an essential ingredient in developing an efficient and profitable business. There are a vast quantity of quality management systems and measures out there and choosing the one will undoubtedly have a dramatic effect on your business.
However, whether that impact is positive or negative will hinge on how well you have done your homework and how closely the system can follow your unique processes.
There are some underlying principles that form the foundation of any quality management system. And whilst there are too many actual systems to discuss in the space we have in this post, we can talk about those principles.
Six Sigma (6σ)
Based on empirical data and statistics, this system works on a defined process to prevent defects. It measures deviation from this process and works to predict the reject rate of finished product based on that deviation.
Critics of the system say that it is only effective in larger businesses with over 500 employees and that it lacks creativity, only being able to support existing processes and has no capability to help implement new systems.
LEAN Manufacturing
This system focusses on the elimination of waste. It supports the identification of this waste by the principle ‘Make obvious what has value by reducing everything else’. It helped Toyota move from being a relatively small manufacturer to being the world’s largest car maker.
The main criticism of the system is its ‘top-down’ approach, meaning that unless managers take the extra step and extra time to consult with the workforce LEAN solutions can look good on paper but be difficult to implement resulting in an underperforming solution.
Overall Equipment Effectiveness
OEE seeks to measure how effective a manufacturing operation is based on a set of operational measurements. It is commonly used in conjunction with LEAN manufacturing to provide an overall set of key performance indicators.
It can have limitations where the skill of the operator is a factor in the quality and/or quantity of outputs. Or where outputs costs can vary throughout the day.
Enterprise Resource Planning
ERP is a beginning to end management system, generally delivered via a software package that attempts to encompass all aspects of a business’ activities.
ERP systems have been supporting back office functions in business since the early ‘90’s, with an increasing focus on customer oriented management, such as integrated CRM systems from 2000.
Due to their comprehensive nature they can be more difficult and more costly to integrate fully into a business requiring a more in depth look at what a business wishes to achieve.
And there’s more
Although quality is often its own reward, there is also the added benefit of being able to tell the world just how seriously you take your commitment to it. The various different ISO accreditations are essentially a badge of honour that you can use to show your suppliers and customers how seriously you take the issue of delivering only the best.
About the author
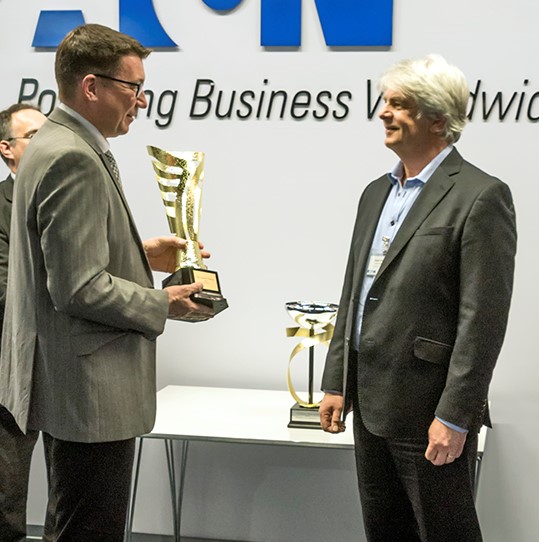
David Chandler
Managing Director
Some say that he taught Thomas Edison all he knew, and that his veins are twin and earth. All we know is: His name is Dave!